How are solar panels made?
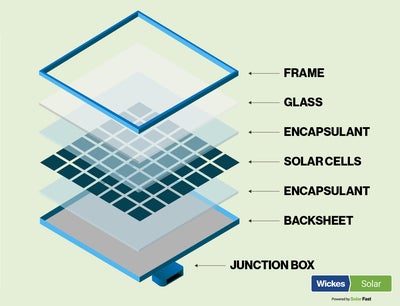
How are solar panels made?
Over the past decade, solar energy has advanced quickly, leading to more efficient energy production. While the basic science has remained consistent, new technology makes all the difference when it comes to getting the best from the materials used. To understand how this technology comes together, let's take a closer look at the process of making solar panels.
Extracting silicon
The journey starts with extracting silicon, the most important material used to make solar panels. It's not as simple as finding it fully formed in the ground; it needs to be extracted from quartz, a type of silicon dioxide found in gravel or stones.
Once the quartz is mined, it's heated to extremely high temperatures in a furnace. A carbon arc is added, which bonds with the oxygen to create carbon dioxide, leaving behind molten silicon. To give the silicon a positive electrical charge, boron is added. Since the silicon still isn’t pure, it’s passed through a heat source several times to remove impurities, creating a refined silicon ingot.
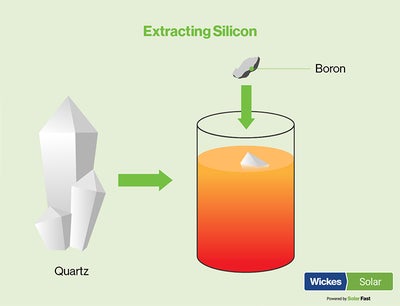
Creating single crystal silicon
The purified silicon is then transformed into single crystal silicon, which can be cut into wafers. This process uses the Czochralski method, where a seed crystal of silicon is dipped into melted polycrystalline silicon and slowly pulled out while rotating. Any remaining impurities stay in the liquid, so we now have 100% pure silicon boule.
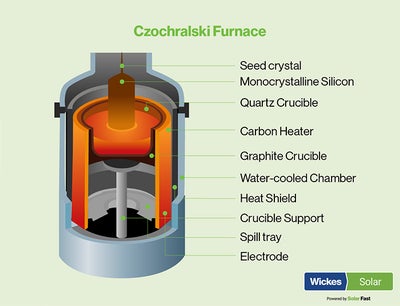
Making wafers
Silicone can’t be used in this form to make solar panels. So next, the silicon boules are sliced into thin discs or wafers. These wafers are often cut into hexagonal shapes to minimise waste, although this can increase costs. Since pure silicon is shiny and reflective, which isn’t ideal for solar panels, a non-reflective film is added to the wafers.
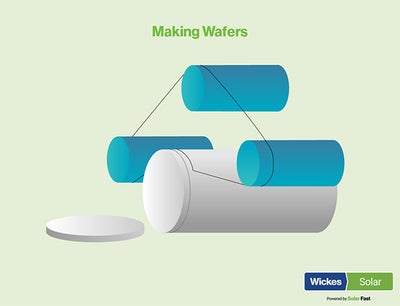
Forming solar cells
With the wafers ready, the next step is to convert them into solar cells capable of turning sunlight into electricity. The wafers are heated and treated with phosphorus, forming a negatively charged layer on top of the silicon. This creates a potential difference when sunlight hits, generating an electric current from the negative phosphorus to the positive silicon boron layer. Conductive wires are then attached to each cell to carry this energy into your home.
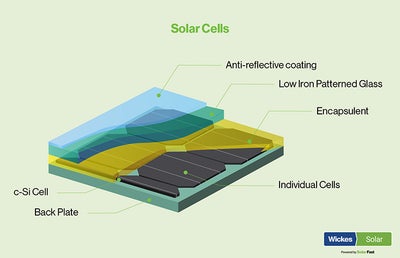
Assembling the solar panel
Solar panels are usually made up of 48, 60, or 72 full cells. However, advancements in technology have shown that splitting these cells can lead to better efficiency. These are known as half-cell panels. Splitting the cells shortens the distance electricity has to travel, reducing resistance. The most common half-cells on the market are the 104 Half Cell panels.
Once the cells, whether half or full, are connected, they are covered with a 6mm thick sheet of glass and backed with a durable polymer sheet, all encased in a frame.
Testing the solar panel
Finally, the assembled solar panels are tested to make sure they meet safety and efficiency standards. They're tested under Standard Test Conditions (STC), simulating ideal sunlight, air mass and cell temperature. Panels are also tested in more realistic conditions that mimic typical outdoor environments.
During the solar panel installation process, Wickes Solar powered by Solar Fast conducts these tests and provides a detailed report in a technical spec sheet.
Are there different types of solar panels?
There are three types of solar panels available on the market, but some are more suited to home installation than others.
- Thin film panels: These panels are flexible but expensive. Unlike other solar panels they can curve to fit around contours on buildings. They have an efficiency of 7% to 18%.
- Polycrystalline panels: The cheapest of the three, polycrystalline panels are made from silicon crystals that are fused together to catch as much sun as possible. This does mean that they’re not as efficient though. They have an efficiency of 13% to 16%
- Monocrystalline panels: These are the panels that you’re most likely to see on houses. While they’re more expensive to make, they are cost-effective as their efficiency makes up for it. They have an efficiency of 15% to 24%.
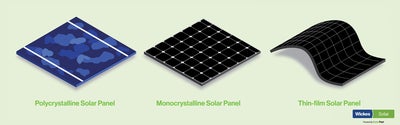
By understanding the detailed process of how solar panels are made, from raw material extraction to the final testing phase, you can appreciate the technology and effort that goes into producing this clean energy solution. To find out more about solar energy, get in touch with Wickes Solar powered by Solar Fast.